When we think about fire safety, what often comes to mind are alarms, fire extinguishers, and sprinkler systems. But behind the scenes, an essential process called fire testing plays a crucial role in keeping buildings, products, and materials safe.
Fire testing evaluates how well materials and systems can withstand and respond to fire, influencing the safety standards that protect us daily. From construction to manufacturing, fire testing impacts numerous industries, setting the stage for safer environments and more reliable products.
In this blog, we’ll dive into the fascinating world of fire testing by exploring surprising facts, lesser-known statistics, and essential information about the testing practices that shape our safety standards. Let’s get started!
12 Fascinating Facts About Fire Testing You May Not Know
1. Furnace temperatures reach 1,000°F in five minutes, 1,700°F in one hour, and up to 2,000°F in four hours.
This rapid temperature escalation replicates the intensity of real-life fires in a controlled setting, challenging materials and structures to withstand extreme heat in short timeframes.
Testing how materials respond at specific temperature intervals helps assess fire resistance and provides insights into how long they might protect occupants and structural elements before giving way.
2. Fire-rated walls require the application of a fire hose stream of 30 to 45 psi for up to five minutes.
Beyond withstanding fire alone, fire-rated walls must also endure a powerful water stream from a fire hose, replicating the cooling phase of firefighting efforts. This test ensures that fire barriers remain intact even when blasted with high-pressure water, preventing the spread of fire and maintaining the integrity of containment.
3. Heat transmitted through a test specimen must remain below 250°F above the initial starting temperature at the average of all critical locations, or below 325°F above the initial starting temperature at any one location.
To prevent the risk of burns and structural compromise, fire-rated assemblies must limit heat transmission.
By capping the permissible heat rise, this requirement ensures that materials don’t dangerously heat the other side of a fire-resistant barrier, which could put people and sensitive equipment in nearby areas at risk. Such strict limits are crucial for ensuring both occupant safety and structural performance.
4. Protection of structural elements must be such that the elements remain below an average temperature rise of 1,100°F.
Structural integrity is at the heart of fire safety; therefore, critical load-bearing elements must stay within an acceptable temperature range to avoid weakening or collapsing under fire conditions.
Limiting the temperature rise to an average of 1,100°F helps ensure that core structural components retain their strength for as long as possible, providing essential time for evacuation and firefighting measures.
5. Fire tests of load-bearing walls and floors must be tested with up to 100% of their full design load applied.
Load-bearing walls and floors need to hold the weight they were designed to carry, even during a fire. Testing them under their full load simulates real-life conditions and helps ensure they won’t buckle or collapse when exposed to high heat and pressure.
6. Flame-spread tests (or tunnel tests) require an induced draft of 240 feet/minute (2.7 mph) inside the chambe%20(1)-1-1-1.jpeg?width=873&height=341&name=NGCTestingServicesIzonPro%20(103)%20(1)-1-1-1.jpeg)
A consistent airflow replicates real-world ventilation conditions, helping evaluate how quickly flames might spread along a surface in a building environment.
The 240 feet/minute air velocity ensures that test results reflect realistic conditions, as air movement can drastically impact flame behavior and the potential spread of a fire. This controlled airflow is critical for determining materials’ flame-spread ratings, guiding their safe use in buildings.
7. Interior finish materials are tested in the corner of a test room using a 30-pound wood crib that generates temperatures up to 1,200°F.
Simulating fire in a confined corner tests how well interior finishes contain or resist flames in the most vulnerable parts of a room.
The 30-pound wood crib represents a real ignition source, pushing materials to withstand significant localized heat without contributing to fire spread. This test is crucial for assessing safety in high-risk areas where fires are likely to start, like kitchens or utility rooms.
8. Combustibility of materials is determined by submerging into an environment of 750°C (1,382°F).
Subjecting materials to extreme temperatures allows testing providers to understand how they react in conditions that could cause ignition or melting. This test measures whether materials will sustain or contribute to a fire, aiding in the selection of safer building materials that won’t fuel flames in a fire situation.
9. Fire testing expansion joints require movement cycling up to 500 times prior to fire exposure.
Expansion joints need flexibility to accommodate shifts in building materials due to temperature changes or structural movement. Testing these joints for up to 500 cycles of movement before fire exposure ensures they remain effective under stress and don’t compromise a building’s fire resistance.
10. To achieve a fire rating, assemblies are tested containing specific materials. We are testing an assembly, not individual materials.
Fire ratings assess how well a complete assembly — such as a wall or floor — can withstand fire, rather than testing individual materials. This holistic approach considers the combined performance of all elements, including insulation, adhesives, and finishes, to ensure the overall safety of the structure.
11. Our wall furnace has 50 gas burners; our floor-ceiling furnace has 80 gas burners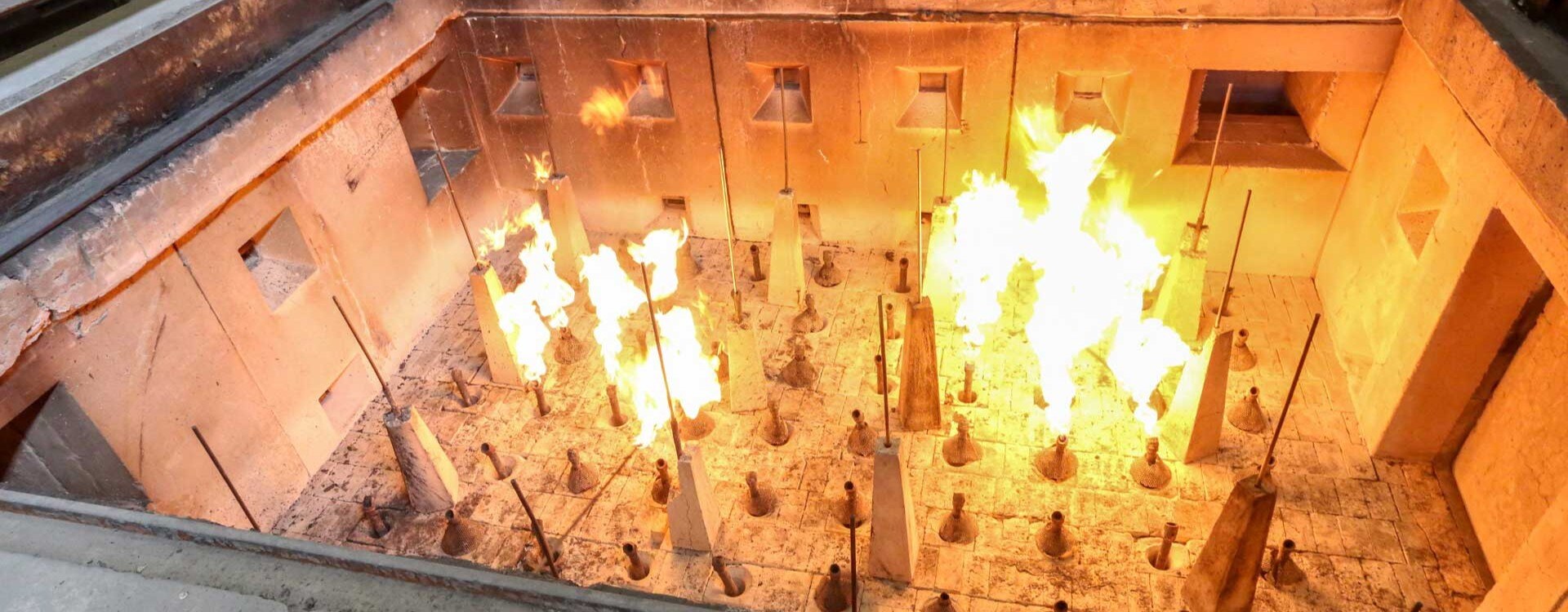
With an extensive number of burners, these furnaces simulate the heat intensity of a severe fire, providing a controlled environment to test the fire endurance of walls and floor-ceiling assemblies.
The high burner count ensures even and thorough heat application, replicating fire exposure across large surfaces and helping our testing providers determine how long materials can resist fire and maintain safety.
12. In NFPA 285, the temperature must stay below 1,000°F at any one of the specific exterior face thermocouples and shall not reach 500°F above ambient 1" from the interior surface of the test assembly within the second-story room.
NFPA 285’s strict temperature limits for thermocouples (devices that measure heat) are designed to prevent fire from spreading vertically through the exterior of buildings.
By capping temperatures at specific points, this test ensures that materials used in exterior wall assemblies don’t ignite or degrade, which is critical for preventing fire spread between floors and safeguarding building occupants on upper levels.
The Value of Rigorous Fire Testing
Fire testing plays an essential role in building safety, providing critical insights into how materials and structures respond to intense heat and challenging conditions.
Understanding these lesser-known facts helps highlight the complexity and rigor involved in the testing process, which is aimed at protecting lives and property. For builders, architects, and property owners, awareness of these testing details can inform better choices in materials and construction practices.
Have questions about fire testing or want to learn more about how NGC Testing Services can support your project? Contact us today — we're here to help you build with confidence and safety in mind.
Search blog articles
Browse by topic
Subscribe for updates
LEARN MORE
Related Blog Articles
GET IN TOUCH
Contact Us
NGC Testing Services features one of North America's most comprehensive and unique fully accredited testing facilities. Contact us today to visit our 50,000-plus-square-foot facility located in Buffalo, New York.