Fire Testing
5 Common Mistakes Manufacturers Make When Preparing for Fire Testing
Fire testing is a crucial step in ensuring the safety and compliance of manufactured products. Yet, despite its importance, many manufacturers overlook critical preparation steps, leading to failed tests, project delays, and even costly product recalls.
To avoid these headaches, it’s essential to understand fire testing standards and take a proactive approach.
This blog highlights five common fire testing mistakes manufacturers make and offers practical tips to improve preparation, ensure compliance, and protect your reputation. Whether you're navigating ASTM standards or refining your product launch, these insights will help streamline your fire testing process for better results.
Understanding the Importance of Fire Testing
Fire testing plays a vital role in manufacturing by confirming product compliance with safety standards and regulatory requirements. Taking the proper fire testing measures ensures that finished products can withstand fire-related risks, keeping consumers safe while meeting important industry regulations.
There are various types of fire testing that certain products must undergo, many of which must adhere to ASTM standards.
Failure to properly test products and materials through the relevant fire testing protocols has significant consequences, including delays in product launches, increased costs due to redesigning and retesting after failure to meet compliance standards, and serious penalties.
Perhaps most damaging of all, failure to include fire testing in product quality assurance procedures could result in product recalls that permanently damage a brand’s reputation.
5 Common Mistakes Manufacturers Make
When it comes to the common mistakes manufacturers encounter, there are a few reasons why these tend to occur, including a lack of knowledge about fire testing requirements, rushed timelines, and inadequate communication with testing experts.
1. Failure to Understand Fire Testing Standards
Because different industries and regions have their own specific fire testing requirements, this misalignment with industry standards can lead to a failure to test and result in manufacturer non-compliance.
To avoid this from occurring, it’s important to properly research all relevant industry standards for fire testing and work with testing experts who can help to make sure your product is fully tested and compliant with all regulations.
2. Incomplete or Inaccurate Documentation
Another issue that can arise is when a manufacturer does not have complete information, such as missing certifications or inaccurate documentation about material details. In these instances, testing labs may reject submissions, which can significantly delay testing schedules and product launch timelines.
To avoid such delays, be sure to keep a comprehensive checklist detailing all relevant documentation for the product, including certifications, material details, and any previous test results.
3. Improper Design & Material Selection
In some situations, manufacturers have selected materials early on in the design process without fully understanding if they will meet fire safety standards. These non-compliant materials will lead to test failure and required redesigns, which can be costly from both a time and financial standpoint for the manufacturer.
Avoid this mistake by working with certified suppliers and conducting pre-testing evaluations of all materials to ensure they will meet the requirements of fire safety testing protocols.
4. Last-Minute Changes to Design or Materials
Similarly, requiring any adjustments late in the production process can invalidate previous testing efforts, so it’s important to lock in design and material specifications early on to avoid these delays and required retesting.
5. Insufficient Pre-Testing Preparation
The last mistake manufacturers often make in preparing for fire safety testing is skipping prototype testing or creating inadequate mock-ups to test on in the first place. These unidentified flaws will emerge during the official testing process, which will result in a failure — and then require redesign and retesting to comply with regulations.
Instead, be sure to conduct thorough in-house pre-testing efforts in a controlled environment to identify any potential issues early on in the process.
Steps to Optimize Fire Testing Outcomes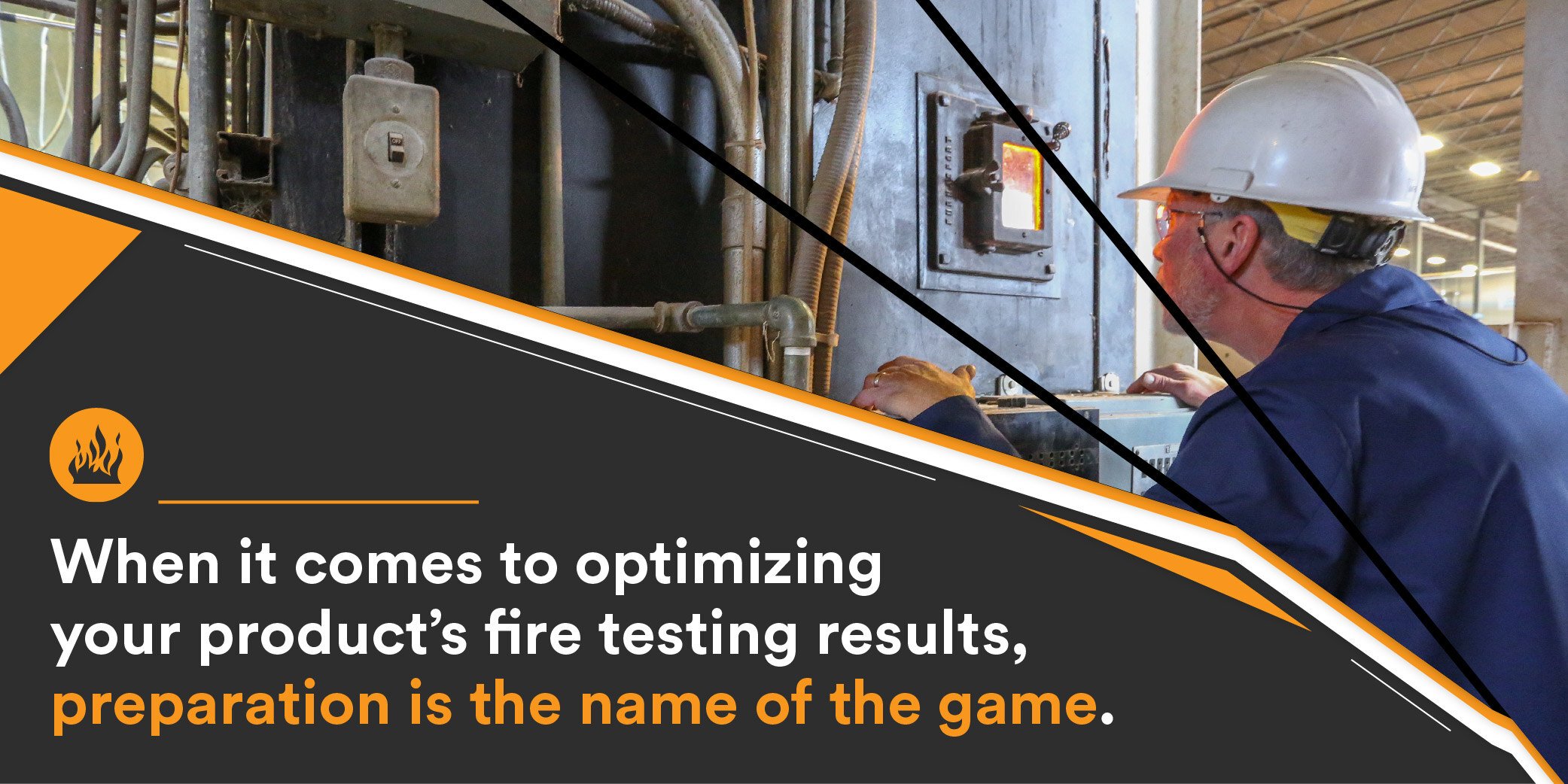
When it comes to optimizing your product’s fire testing results, preparation is the name of the game. Here are five things you can do to improve your product’s fire safety testing outcome:
- Work with a team of experts from the start: Consult with a certified testing lab as early as the product design phase to ensure all aspects align with fire safety standards.
- Understand and apply all relevant standards: Conduct internal audits to ensure compliance with your industry's specific fire testing requirements.
- Build testing into your product launch timeline: Allow sufficient time for testing, including potential retesting, to avoid rushed deadlines and missed compliance.
- Don’t forget to document everything: Organize all specifications, certifications, and test results in a centralized, accessible system.
- Conduct pre-testing in a controlled environment: Run internal tests to identify and address failure points before submitting products for official testing.
Uncovering the Benefits of Proper Fire Testing Preparation
Properly preparing for fire testing comes with its own set of unique benefits, all of which help to get a new product to market faster and keep consumers (and a manufacturer’s brand reputation) safe at every turn.
Here are just a few ways taking the time to prepare for fire safety testing significantly benefits a manufacturer at every step of the process.
Faster Certification Process
Avoid delays caused by failed tests or incomplete documentation by ensuring all requirements are met before submitting your product for testing. A comprehensive submission allows testing labs to evaluate your product efficiently, which will reduce the time to certification.
Reduced Costs
Minimize expenses associated with retesting, redesigning, and any associated potential fines for non-compliance. Investing in your product’s preparation upfront can save significant resources in the long run by avoiding unnecessary setbacks and ensuring a smoother path to market — and less stress along the way!
Enhanced Confidence
Deliver a safe and compliant product that meets both your customer’s and regulatory authority’s expectations. Going the extra mile in your design and QA process builds trust with stakeholders and demonstrates your commitment to safety and quality.
Improved Product Reputation
Ensuring compliance through your thorough preparation efforts also helps establish your brand as a reliable and safety-conscious manufacturer, which then enhances customer trust and loyalty. A well-tested product is less likely to face recalls, preserving your brand’s image in the market.
Streamlined Production Timelines
By addressing potential issues early in the design phase and incorporating fire testing into your project schedule, you can avoid any rushed adjustments and keep your production timeline on track right from the start.
Set Your Fire Testing Up for Success
In the end, avoiding common pitfalls in fire testing preparation saves time, reduces costs, and ensures your product’s success. Proactive measures, such as engaging with experts early, maintaining thorough documentation, and prioritizing pre-testing evaluations, make a significant difference.
With these steps, you can confidently bring compliant, high-quality products to market while minimizing risks and maximizing efficiency.
Have questions about the best way to avoid these common mistakes when fire testing? Contact NGC Testing Services to get started.
Search blog articles
Browse by topic
Subscribe for updates
GET IN TOUCH
Contact Us
NGC Testing Services features one of North America's most comprehensive and unique fully accredited testing facilities. Contact us today to visit our 50,000-plus-square-foot facility located in Buffalo, New York.